A significant contribution to Warrington Town Centre’s Regeneration.
This prestigious project tackled the re-build of a multi-storey car park that would function as the gateway to the £142m regeneration and development of Warrington Town Centre – now known as ‘Time Square’. The works comprised of the demolition of the existing car park and construction of a new 1165 space, 8 floor multi-storey car park for Warrington Borough Council.
The challenging substructure and superstructure works were finished to the highest of standards meeting the quality specifications. This quality is exhibited in the glass door lifts and the anodised aluminium, terracotta and rainscreen stone façade.
This car park is the primary public car park for the new Time Square town centre redevelopment and incorporates car parking provision for the new council offices.
Warrington Borough Council
Warrington, England
£20M
60 Weeks
Key Challenges.
Demolition of the existing multi-storey car park and construction of the new car park took place within Warrington Town Centre, surrounded by the strategic road network which could only be closed for short durations.
To successfully construct the car park within the site footprint we secured existing offices opposite the site for our project offices, eliminating the need for site offices within the site footprint. We allowed time in our programme to demolish the existing car park in its entirety.
We worked meticulously to develop a detailed, multi-phased construction methodology with our supply chain to successfully maintain site access and egress, craneage, plant, and materials supply throughout the works.
With so many interfaces within the detailed design – foundations, lifts, stairwells, structural steel, cladding, mechanical and electrical – it was clear that a coordinated approach was required. In addition to a dedicated Design Coordinator, we implemented a Common Data Environment specialist to improve the exchange of technical information.
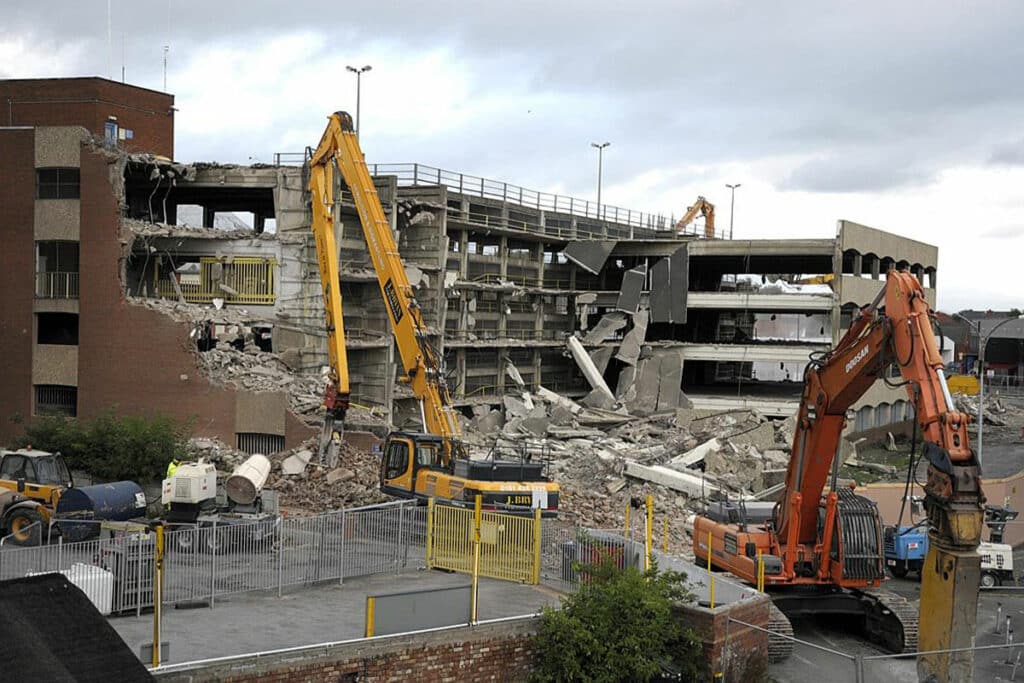
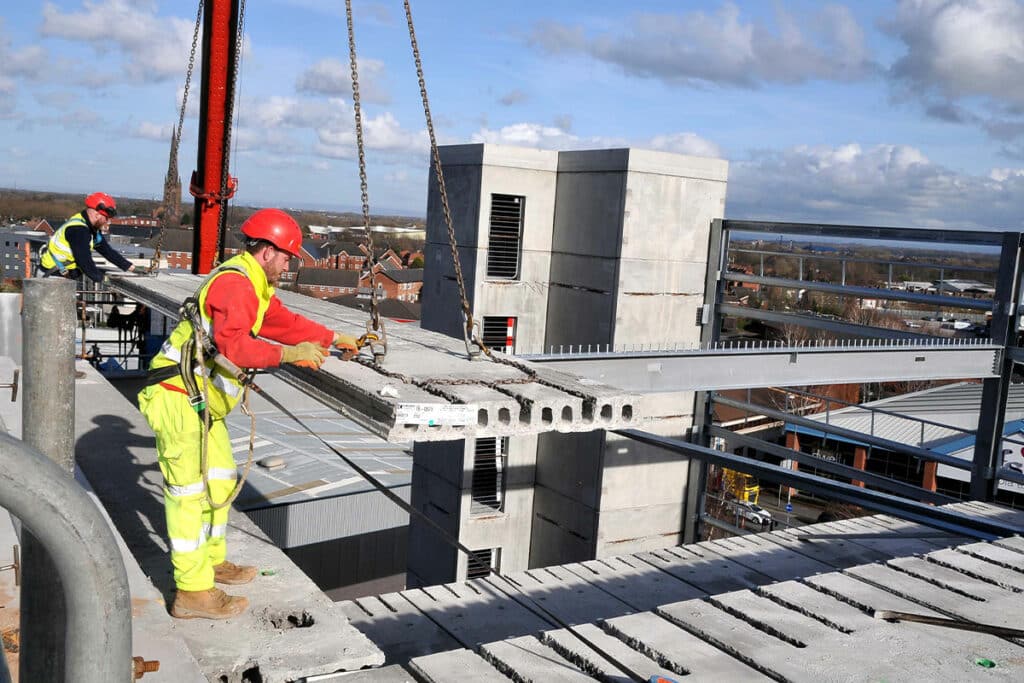
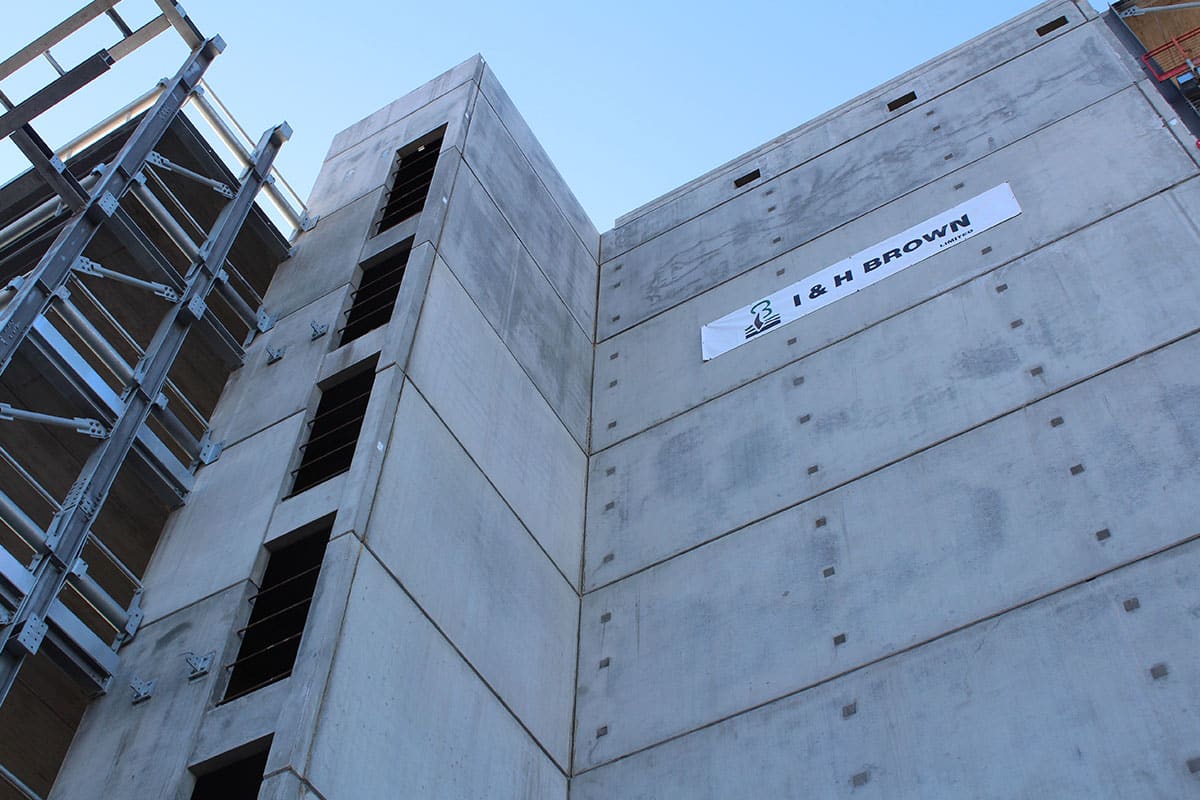
Our Solution.
The existing multi-storey car park was constructed almost entirely of reinforced concrete. Once demolished, we crushed and screened the concrete into 6F2 and retained this material on site temporarily as the piling platform, then permanently within the ground floor construction. Only the reinforcing steel was taken offsite and was recycled. This approach reduced the carbon impact of the project by reducing transportation of waste and imported aggregates. This aspect of the project helped us win the Construction Recycler of the Year Award at the National Recycling Awards.